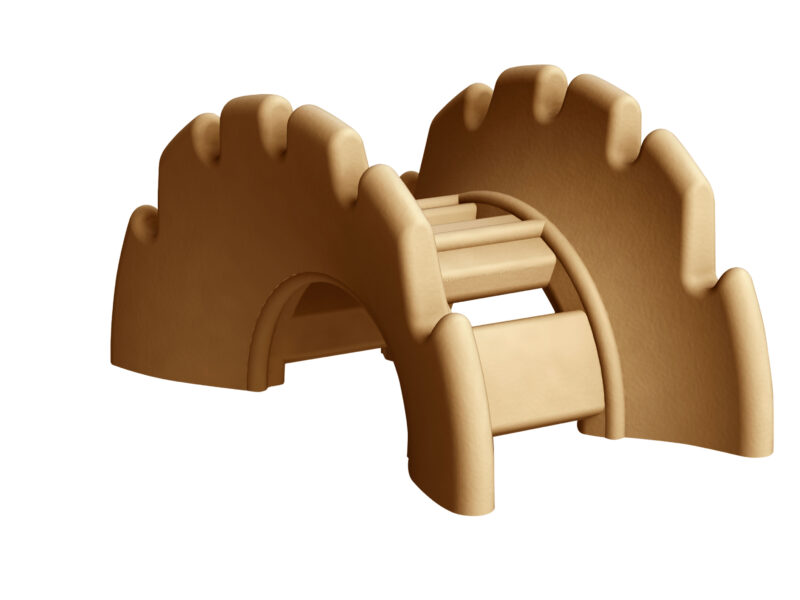
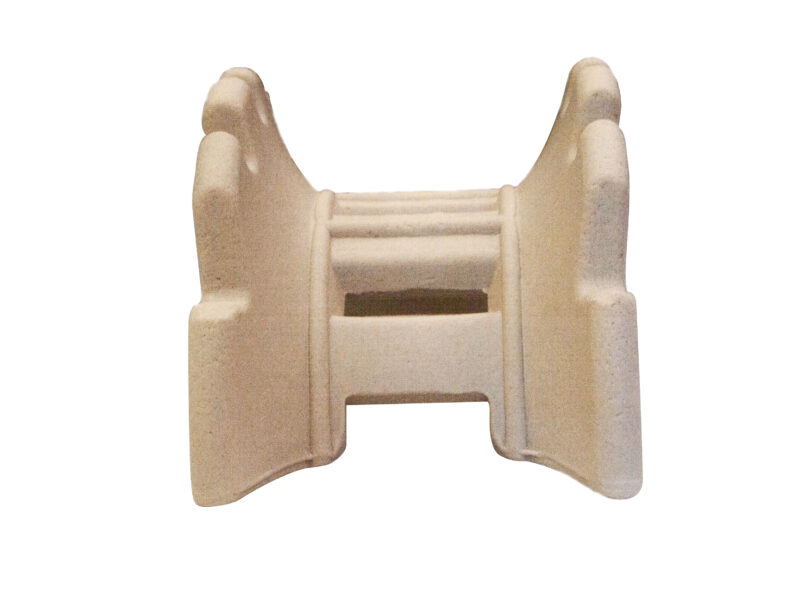
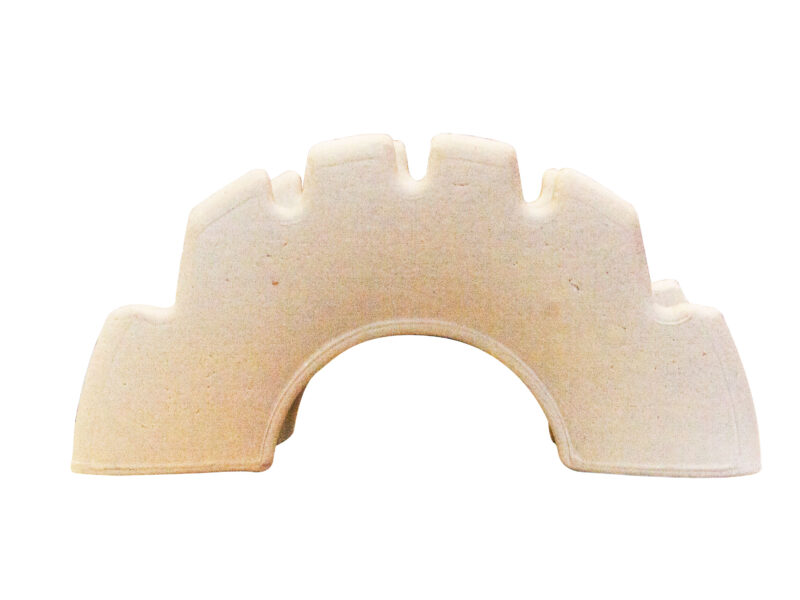
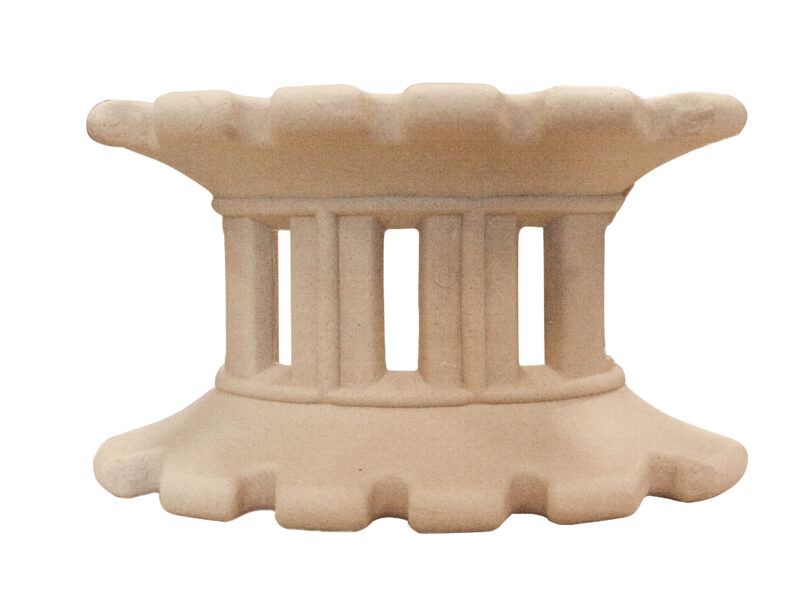
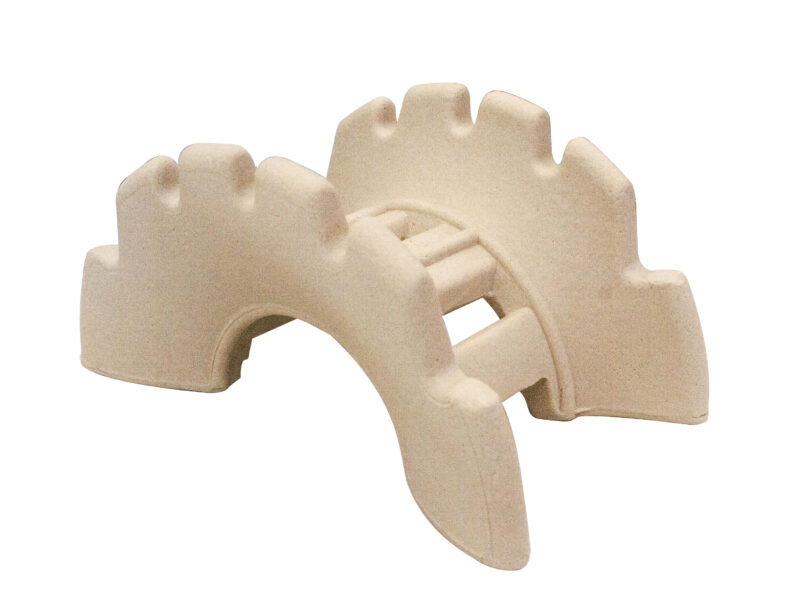
The random packing MaxiSaddles® BPC (MaxiSaddle Low Pressure drop) is the newest generation belonging to the MaxiSaddles ceramic saddle group. Its modern design features a greater number of gas passage points, increasing efficiency and decreasing pressure loss, making it ideal for process revamp.
Its highly effective area and low resistance to gaseous flow, minimize head loss and enhance the packed bed in terms of capacity and efficiency. Its special composition has excellent mechanical and chemical properties.
MaxiSaddles® BPC ceramic packing are manufactured by Clark Solutions in Brazil and due to its modern design, it was necessary to implement a manufacturing method different from that of the common MaxiSaddle®, which gives an excellent surface finish. Both go through the same strict composition quality controls, mechanical strength and dimensional compliance.
MaxiSaddle is used for exchange at the gas-liquid interface, so the larger the contact area between the phases, the better the absorption efficiency.
To provide a high contact area between the phases, MaxiSaddle® was created. Studies have led to the conclusion that it would be possible to relieve the resistance to gas flow by changing the geometry to what we now know as MaxiSaddle® BPC. Its design avoids stagnation and back-mixing zones, reducing head loss without compromising efficiency.
MaxiSaddles® BPC ceramic saddles are randomly distributed below the liquid dispenser and above the Cross-Partition Ring, which in turn are supported by the MaxiDome.