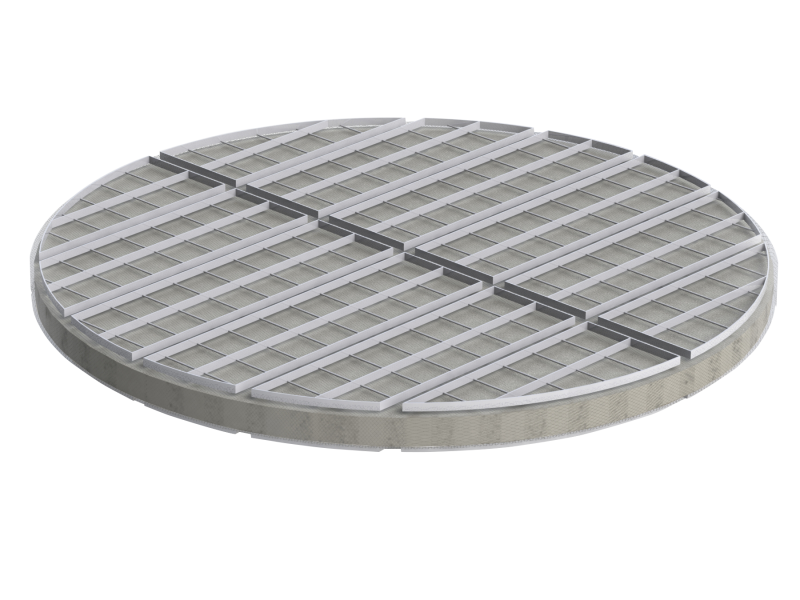
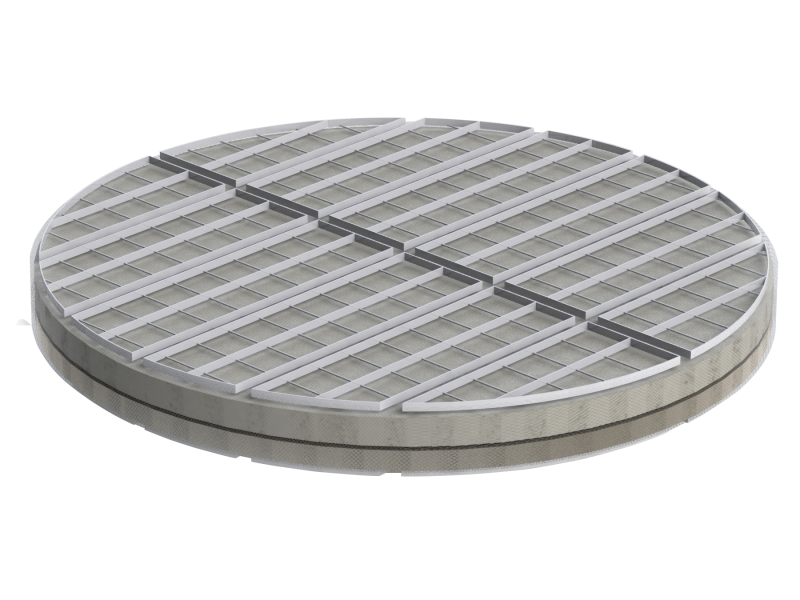
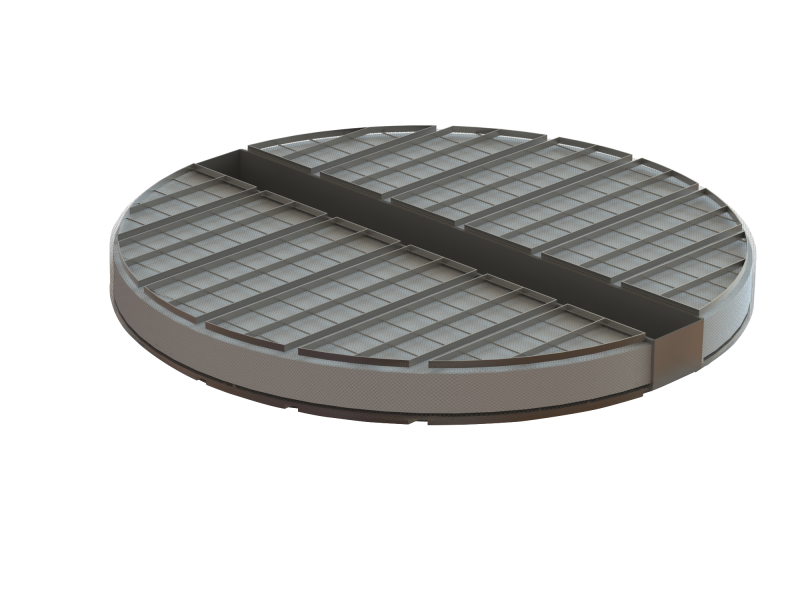
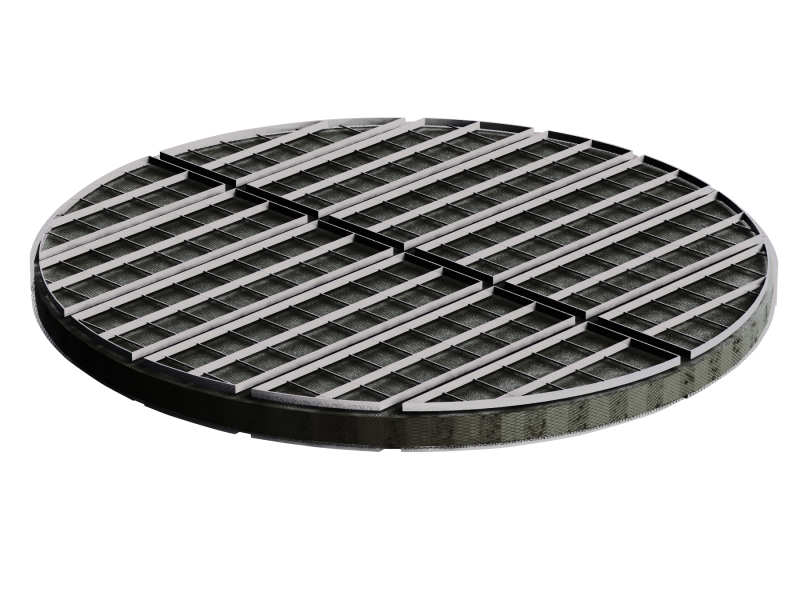
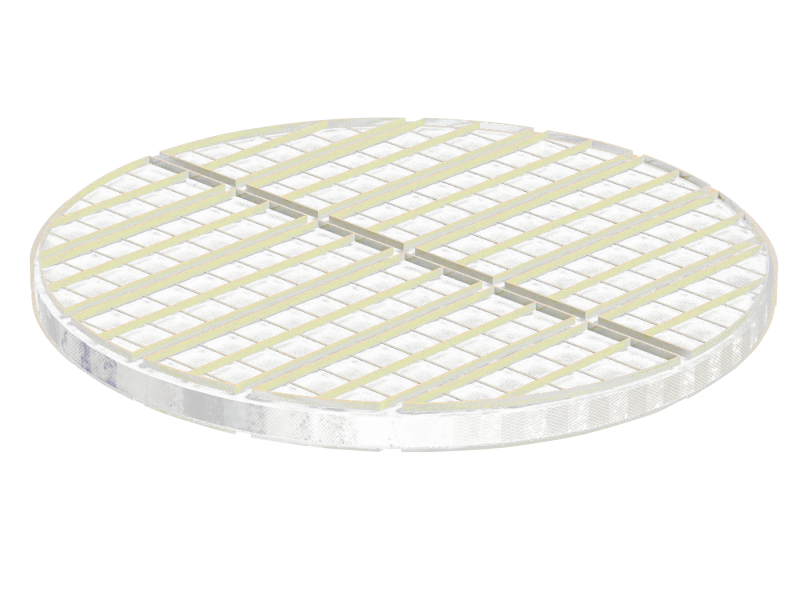
MaxiMesh® mist eliminators consist of a mesh formed by extremely fine knitted (or co-knitted) threads that have a very high void percentage.
Clark Solutions developed and improved a new model family, which replaced the old 1951 models on the market. These models were developed based on a vast knowledge about the behavior of fiber eliminators and designed for the needs of the chemical industry, such as:
MaxiMesh® in SX and PTFE, in double zone (metallic zone + co-marked zone) widely used in the Sulfuric Acid industry, to capture smaller particles, without affecting the capacity and increasing the life of the equipment in extremely corrosive media.
The MaxiMesh® plus technology has the highest capacity when compared to high performance mist eliminators. MaxiMesh ®Plus consists of a MaxiMesh® oriented in series with a MaxiChevron® or HeliFlow®, in order to combine the greater capacity of these with the high efficiency of the former.
The MaxiMesh® plus technology has the highest capacity when compared to high performance mist eliminators. MaxiMesh ®Plus consists of a MaxiMesh® oriented in series with a MaxiChevron® or HeliFlow®, in order to combine the greater capacity of these with the high efficiency of the former.
MaxiMesh® is the Clark Solutions equipment that contains the largest number of models. This is due to the number of application possibilities in the industries, since it has a high performance proven in all its uses.