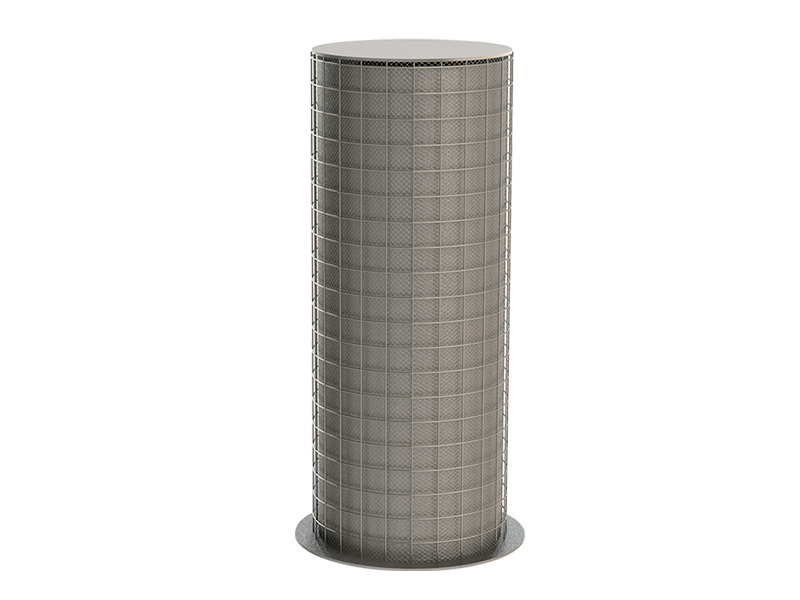
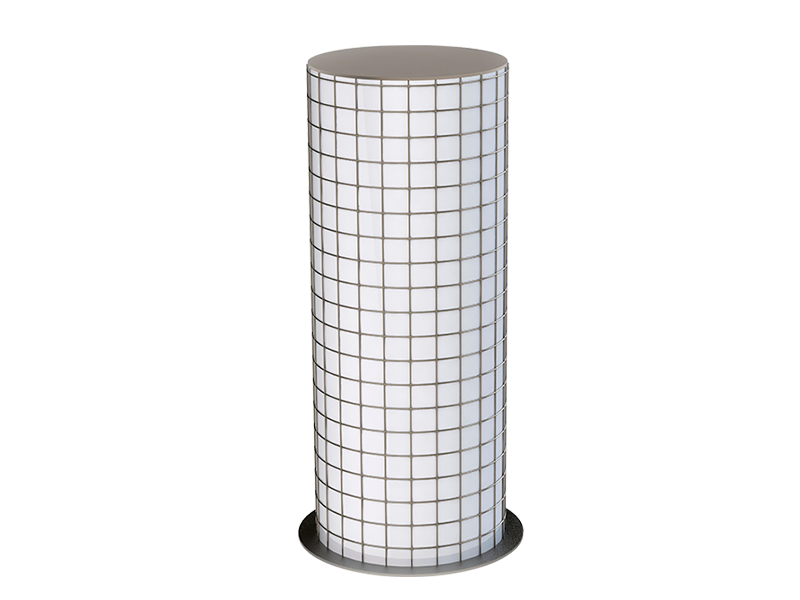
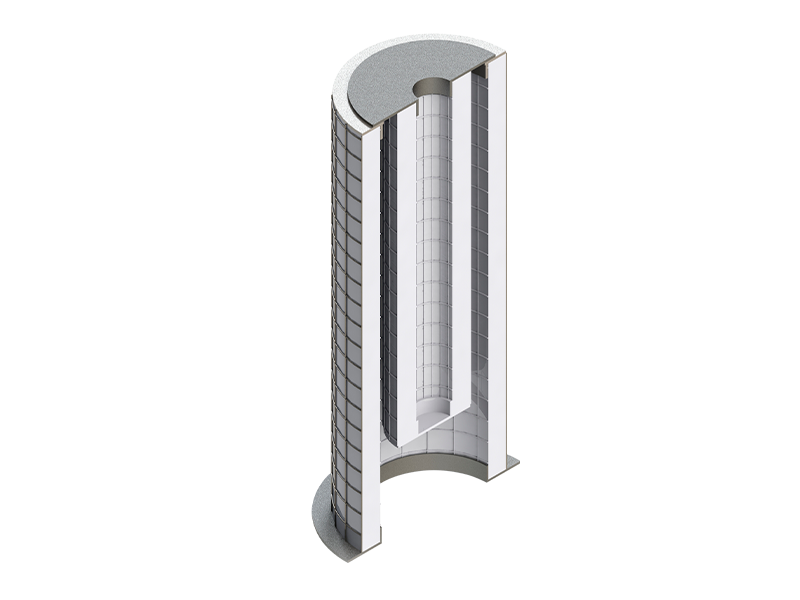
Los eliminadores de niebla de lecho de fibra FiberBed® están diseñados para eliminar las partículas de niebla, que son pequeñas gotas de líquido presentes en una corriente de gas a través de lechos de fibras de vidrio, poliéster, polipropileno u otros polímeros.
Los lechos se compactan entre pantallas cilíndricas coincidentes o placas paralelas, con el fin de distribuir aleatoriamente las fibras de diámetros definidos y con las densidades necesarias para lograr la eficiencia de captura y pérdida de carga de diseño.
Las partículas de 3 micrones o más se recogen cuando su momento (energía cinética) les impide seguir las líneas de corriente de gas alrededor de una fibra. El momento de la partícula hace que permanezca en su camino hasta llegar a la fibra donde es capturada.
Dado que el impulso es una función de la masa y la velocidad de la partícula, se deduce que las gotas grandes se recolectarán de manera más eficiente que las gotas pequeñas que viajan a la misma velocidad. Este tipo de mecanismo depende en gran medida de la inercia de las partículas y la viscosidad del gas.
Algunas partículas siguen el camino del gas, pero debido a su diámetro acaban «tocando» las fibras del lecho, donde se acumulan. Mecanismo poco dependiente de la inercia, las partículas y la viscosidad del gas.
Las partículas subcrómicas se recogen cuando su momento (energía cinética) les impide seguir las líneas de corriente de gas alrededor de una fibra. El momento de la partícula hace que permanezca en su camino hasta llegar a la fibra donde es capturada.
Dado que el impulso es una función de la masa y la velocidad de la partícula, se deduce que las gotas grandes se recolectarán de manera más eficiente que las gotas pequeñas que viajan a la misma velocidad. Este tipo de mecanismo depende en gran medida de la inercia de las partículas y la viscosidad del gas.
El FiberBed® Mist Eliminator se puede aplicar a varios procesos, en la protección de equipos o control de emisiones atmosféricas. Sus principales aplicaciones son aquellas donde existen partículas pequeñas, menores a 3µ, y donde exigen altas eficiencias de recolección, normalmente superiores al 99% de las partículas.
Desarrollado para recolectar 75-99% de partículas en el rango de 1 a 3 micrones. El impacto inercial se utiliza como mecanismo principal y de captura y, por lo tanto, está desarrollado para operar a altas velocidades en el lecho (en el rango de 1.0 a 3.0 m / s).
Los cilindros de impacto tienen típicamente 650 mm (26 ”) de diámetro y 500 mm a 1500 mm de altura (20-72”).
Se fabrican utilizando técnicas modernas y control computacional prácticamente sin contacto humano. La fabricación informatizada permite un seguimiento continuo de la pérdida de presión durante el proceso de fabricación. No todos los materiales disponibles se fabrican de manera que puedan ser informatizados.